Soda Recovery Boiler
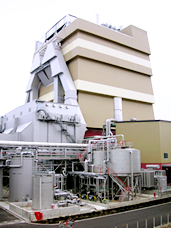
The Soda Recovery Boiler is a rational facility with energy- and resources-saving systems by utilizing the lignin for an energy source and recovering solvent (soda). The boiler burns a mixture of cooking chemicals and the lignin residue (black liquor) remaining after separating pulp (cellulose) from dissolved wood at a pulp and paper mill. And recently this system enjoys a high reputation as a superb CO2 reduction technology making use of biomass fuels also from global environmental aspects. Kawasaki has delivered approximately 100 boilers since its first supply of the Soda Recovery Boiler for a pulp and paper mill in 1949, having a history of the soda recovery boiler in Japan. We have always supplied recovery boilers to meet users' need--beginning from the Murry Waren-type recovery boiler to the spray-type, Scandinavian odorless-type, and single drum-type boilers for high pressure and high temperature steam.
Features
The capacity of a recovery boiler is getting larger year by year, reaching the maximum handling capacity of black liquor: 2, 900 t/d, and the boiler evaporation capacity: 475 t/h at the latest plant. And due to the improvement of anticorrosion technologies, the steam pressure and temperature have reached 10.3 MPa and 505 deg.C respectively. Many technologies unique to recovery boilers are employed based on long experiences and a track record. For example, black liquor is sprayed at a low pressure to ensure burning in the combustion chamber and soda recovery. Air is supplied in 4 stages, and anticorrosive materials and composite tubes are adopted so that combustion gas of black liquor containing highly corrosive elements such as Na, S and Cl in plenty won't damage the boiler. This has achieved superb safety, long continuous operations, highly-efficient chemical and heat recovery, energy-saving and low pollution.
Contact
If you need more information about our business,
please feel free to contact us.