Reducing Airframe Weight
Reducing the airframe weight is an essential factor in improving the basic performance of an aircraft. Producing designs that minimize the airframe weight has proved to be a challenge ever since the first airplane was built.
This section describes KHI technologies for minimizing the weight of the airframe while ensuring that it has sufficient strength to withstand the loads exerted on it during operation.
Composite material used in the Boeing 787
KHI is part of the international consortium that has contributed to the development and manufacture of the Boeing 787. This innovative aircraft was designed to deliver approximately 20% better fuel efficiency than conventional commercial airplanes in the same class by adopting the latest high-efficiency engine and using composite materials for about 50% of the airframe weight. In its manufacturing of the forward fuselage, KHI has achieved a world first by using a large single-piece structure made only of composite materials.
The manufacturing method used by KHI is also completely different. Resin-impregnated carbon fiber sheets are laminated in a cylindrical shape and cured in a large autoclave (pressure oven) to create a seamless fuselage.
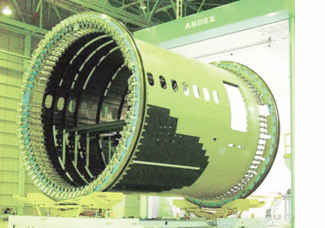
Forward fuselage of the Boeing 787
Manufacturing and Processing Technologies for Light Airframes
Airframe parts are designed to have an optimal shape and thickness in order to minimize their weight while maintaining their strength. By employing a large number of large-scale specialized systems, KHI is able to deliver improved precision and reduce the manpower requirements in the manufacturing and processing of each part.
Rivet connection technology is a typical example of a manufacturing technology that makes use of large-scale specialized facilities.
Since aircraft are typically operated for 20 to 30 years, reliability and durability must be ensured even for the rivet connections. Consequently, KHI manages this process very strictly.
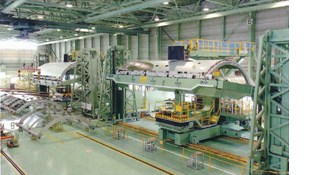
Five-axis NC auto tacker