Improving Aerodynamic Performance
Wind tunnel tests were first used when the Wright brothers designed the Wright Flyer. However, since many modern aircraft now travel close to the speed of sound, it has become necessary to construct more complex, large-scale facilities and adopt more advanced testing and measurement technologies.
KHI develops aircraft using its own proprietary transonic wind tunnel facilities that can achieve velocities of up to 1.4 times the speed of sound.
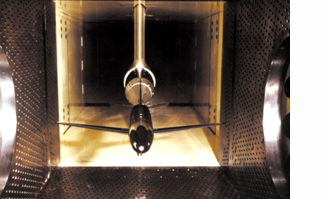
Testing in a KHI transonic wind tunnel
We also constantly strive to improve the wind tunnel test system itself. Our accomplishments include the development of the trisonic wind tunnel (Acquisition, Technology & Logistics Agency), which is one of the world's largest blowdown wind tunnels.
This wind tunnel test system controls the high-speed flow of air with a high degree of precision within the following ranges: subsonic (0.3–0.8 times the speed of sound), transonic (0.8-1.4 times the speed of sound), and supersonic (1.4-4.0 times the speed of sound).
In addition to the wind tunnel test system itself, we are also developing special test equipment for use inside the wind tunnels.
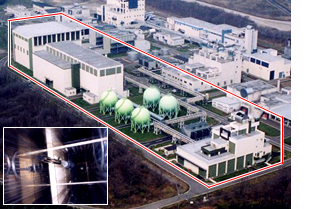
Panoramic view of the trisonic wind tunnel system
(Source: Acquisition, Technology & Logistics Agency)
Wind tunnel tests enable us to identify physical phenomena directly, but they are expensive and time consuming. Consequently, the use of computational fluid dynamics (CFD) analysis technology (also known as the "numerical wind tunnel system") has become increasingly important in recent years.
We were one of the first companies to identify the potential of CFD analysis technology. Having developed our own CFD software over the past 30 years, we have been able to produce more precise aerodynamic designs.
The increased precision of our aerodynamic designs was achieved by comparing our CFD analysis with the results of wind tunnel tests to verify its accuracy and by growing our expertise.
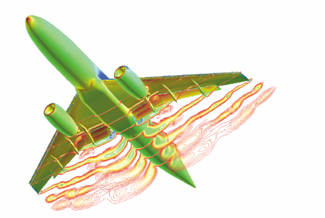
Example of CFD analysis for a high-lift system