Product Safety and Quality
Management Approach
Our Basic Stance
The Kawasaki Group’s businesses involve the provision of many infrastructure products, so ensuring that customers can use our products and services with confidence is a key management issue. In a section titled “Quality and Safety of Products and Services,” the Kawasaki Group Code of Conduct states that we must provide high-performance, high-quality, and safe products and services. We will constantly maintain a high level of trust in the Kawasaki Group and contribute to the quality assurance of management by creating a Group-wide quality-assurance and product-safety structure, producing safe and excellent products that meet the expectations of our customers, and supplying appropriate services.
Product Safety and Quality Policy
The Kawasaki Group recognizes that creating new value contributing to people’s affluent lives and the future of the global environment is our social responsibility and that supplying products and services with customer-satisfying quality is one of the Group’s management principles relating to business continuity. In 2021 we established the Kawasaki Group Policy on Quality Management, which is operated properly throughout the entire Group so as to continue activities effectively and efficiently toward the creation of customer value.
Scope of Policy Application
The Kawasaki Group
Structure
We have established the TQM* Department within the Corporate Technology Division and are promoting Group-wide quality-assurance activities centering on policy management, daily management, quality assurance by process, and quality management education and training based on the TQM approach. We have also established divisions responsible for quality control in each business segment so as to promote quality-improvement activities within these business segments.
* Abbreviation of Total Quality Management
Support for the building of best-suited TQM promotion system for each business segment
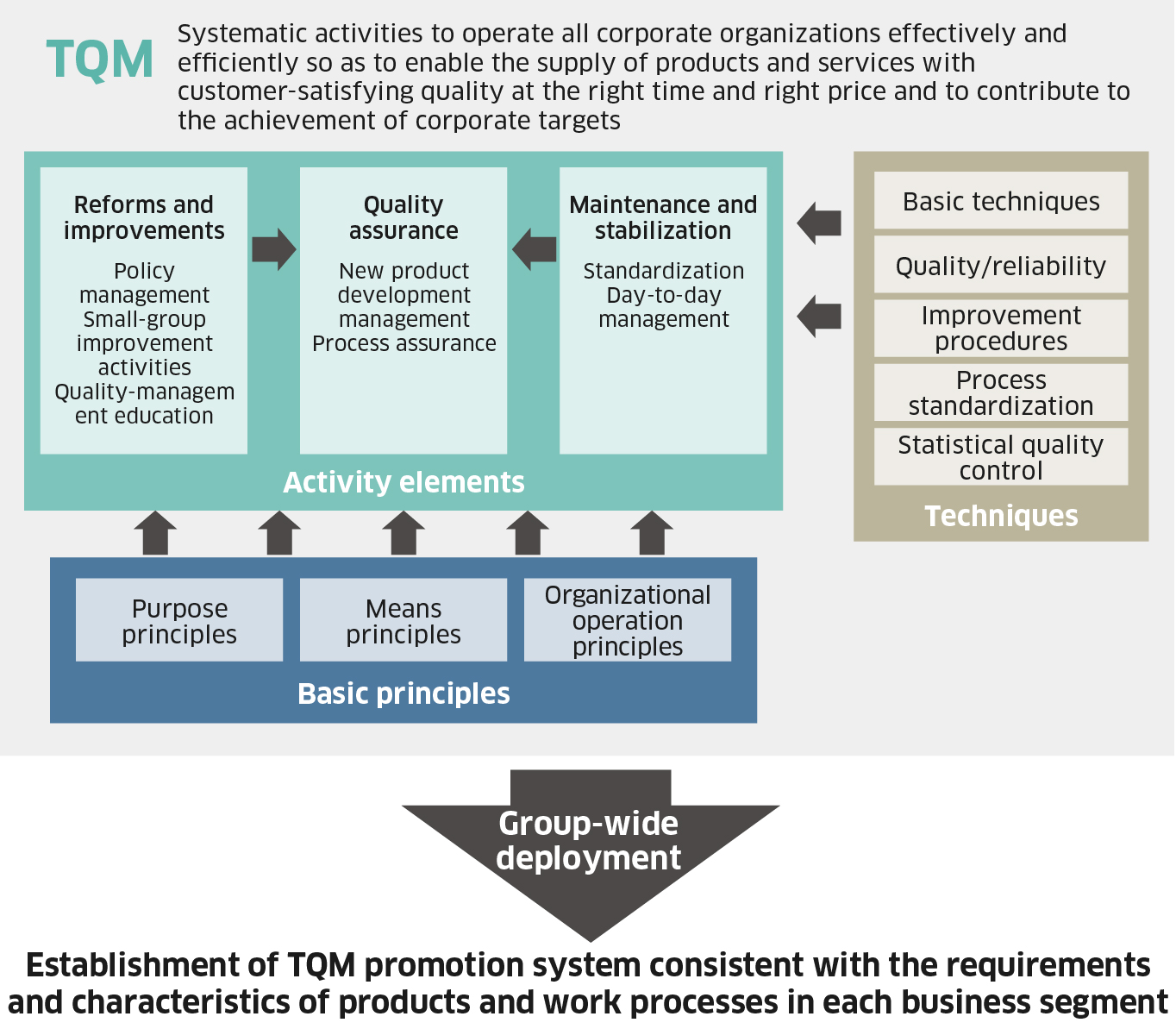
Responsible Officer
Hiroshi Nakatani, Representative Director, Senior Corporate Executive Officer (in charge of TQM)
Responsible Executive Organ and/or Committee
We promote initiatives by regularly formulating policies, plans, and so on related to the building and strengthening of the Group-wide TQM promotion system, including quality assurance. Furthermore, we promote information sharing between the Head Office and business segments and TQM activities through meetings of the Company-Wide Quality Committee held four times a year.
Product Safety and Quality Management
We have built a quality-assurance system that, for each business segment and product group, clarifies the roles of each division relating to quality assurance at every stage, from product contract, development, and design to after-delivery service, and enables the production of safe and excellent products and the implementation of appropriate services that satisfy customers. This quality-assurance system includes the following:
- A clear understanding of the product quality (function, safety) demanded by customers and society
- The planning and development of products that meet the above demands
- The setting of criteria, standards, etc.
- The review of contract content
- Appropriate document management
- Weaving of demanded quality (function, safety) into design
- Crafting of design quality into products through appropriate production planning and management
- Guidance and management of quality-assurance activities of suppliers based on appropriate procurement plans
- Reflection in customer services, development, design, and manufacturing through the gathering, understanding, and analysis of after-delivery quality information
- Quality-assurance auditing (including suppliers)
- Effective quality-assurance educational programs and raising of quality-assurance awareness
- Promotion of the most effective and economical quality-assurance activities through the appropriate utilization of management technology
ISO 9001 Certification Status
The Kawasaki Group acquires ISO 9001 certification at the level of business segments or Group companies, with approximately 70% of domestic and overseas production sites having obtained this certification.
- Aerospace Systems Company: Certified (JIS Q 9100 for Defense & Aerospace, Commercial Aircraft, Helicopter & MRO, and Aero Engine Business Division)
- Energy Solution & Marine Engineering Company: Certified (Energy Solution, Plant Engineering, Marine Machinery, and Ship & Offshore Structure Business Division)
- Precision Machinery & Robot Company: Certified (Precision Machinery Business Division and Robot Business Division)
- Kawasaki Railcar Manufacturing Co., Ltd.: Certified
- Kawasaki Motors, Ltd.: Certified
|
Promotion of TQM Activities
- Promotion of quality-assurance activities and TQM activities in business segments
We position TQM as an approach toward supplementing and strengthening quality-assurance activities in business segments. Rather than individual activities, we tackle activities as a means of enhancing the quality and efficiency of company-wide work and services using the TQM approach. - Implementation of company-wide seminars, etc. to disseminate TQM
We continuously implement level-specific seminars for all employees. In addition, we deepen understanding of TQM at all levels, from new recruits to top management, by means of a level-specific educational curriculum including the use of our original teaching materials and seminars with outside speakers. - Evaluation of TQM levels
We implement the evaluation of TQM levels and, using common indicators, quantitatively assess the state of implementation of TQM activities in all business segments and at Head Office divisions. Through these surveys, we assess the current state of implementation of TQM activities and identify processes and activities where improvements are desirable, which leads to the sharing of our respective strengths.
Education and Awareness Raising on Product Safety and Quality
We implement TQM education for all employees and at all levels in an effort to raise awareness of quality. In each business segment and for each product group, we conduct education for employees actually involved in manufacturing on quality and product safety depending on product properties, thereby endeavoring to improve quality and ensure product safety.
Measures in the Event of Product Quality Defects and Incidents
We monitor the status of quality defects and incidents involving Kawasaki products, ensuring that required countermeasures are being implemented and reflecting findings to enhance our quality management systems.
In the event of quality defects or incidents with a grave impact on our customers or on society, or major quality defects or incidents which significantly undermine trust in the Group, these are reported as expeditiously as possible to both the President and the supervisory departments at Head Office. Such defects and incidents are additionally reported to the Corporate Communications Group and other relevant departments, with notifications issued and information disclosed to the competent authorities.
Contact
If you need more information about our business,
please feel free to contact us.