1990-
History of Kawasaki
1991
Tunnel boring machines successfully complete work on the Eurotunnel.
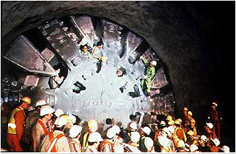
In July 1987, Kawasaki received an order for two tunnel boring machines (TBMs) with diameters of 8.17 meters for the underwater railroad for the Channel Tunnel linking Great Britain and the European continent. These machines were to excavate part of the two underwater tunnels from the coast of Sangatte in Northern France to the British coast. Due to the chalk strata on the French coast partly leaking with some faults, a sudden inflow of high-pressure water was expected during construction. In addition to these complex strata 40 meters under the sea and a high water pressure of a maximum 10 atmospheres, continual high-speed boring of 16 km at 500 m per month was also required. The difficulties become clearer when compared with the commonly accepted conditions for a TBM project: several km of boring at 200 - 300 m per month under a pressure of 1 - 2 atmospheres.
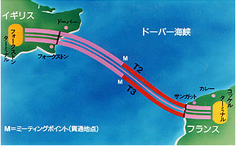
Furthermore, the leadtime from contract to design, manufacture and delivery was also set at only 13 months. However, because Kawasaki is a leading manufacturer of shield machines and TBMs, it aggressively surmounted these difficulties, supported by its expertise and track record for around 1,000 of these products. It was in June 1988 that the two machines were shipped from Kawasaki's Harima Works with more than 10,000 parts and underwent test runs.
1996
Excavation on the Tokyo Bay Aqua-line is completed by the world's largest shield machines
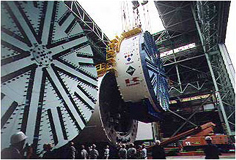
During the Tokyo Bay Aqua-line construction, eight shield machines were used to excavate the underwater tunnel on the Kawasaki City side. Kawasaki manufactured three shield machines out of those, with a diameter of 14.14m - the largest class in the world. 1,200 cutter bits, made of ultra-hard alloy, excavated the earth with the cutter face fully rotating once every 2.5 minutes. Completely automated machines enabled single man operation, adopting Kawasaki's proprietary automated system to assemble segments, or the blocks formed of reinforced concrete to be placed against the tunnel walls.
1996
100th anniversary
2001
Opens state-of-the-art, fully integrated rolling stock factory unique in the U.S.
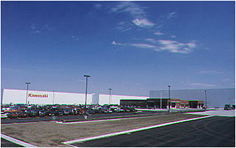
In 2001, the Company opened the U.S.'s first fully integrated rolling stock factory inside Kawasaki Motors Manufacturing Corp. U.S.A. (KMM)'s Lincoln Plant in Nebraska, with production beginning the following year. The layout of the new factory, which occupies a 40,000 m2 structure at the KMM Lincoln Plant's 1.36 km2 facility, has fabrication and outfitting lines that stretch 480 meters and which integrate body fabrication, testing, painting and outfitting in a single stream from entrance to exit. Because the factory uses rubber-wheeled and air-lift trucks to maneuver production cars within the factory, the factory floor is completely flat and free of rails. These features make the new factory more efficient and flexible, not only by facilitating the flow of production cars, components, and other materials, but also by making it easy to rearrange the factory layout based on the type of car to be manufactured next.
2001
Introduces an internal company system and an executive officer system.
2002
Kawasaki Shipbuilding Corporation and Kawasaki Precision Machinery Ltd. are established as wholly owned subsidiaries.
2004
Ships first 700T train to Taiwan High Speed Rail
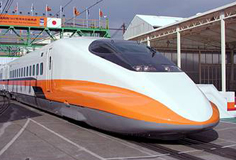
The Taiwan Shinkansen Corporation (TSC), comprising seven Japanese companies including Kawasaki, shipped the Taiwan High Speed Rail Corporation its first 12-car high-speed train. Taiwan High Speed Rail is the first overseas project to use Japan's Shinkansen technology, and the 700T-model train is the first Shinkansen train ever shipped overseas. The 700T, based on the 700-series Shinkansen train jointly developed by Central Japan Railway Company and Western Japan Railway Company, has been optimally configured for Taiwanese geography, climate, legal regulations, and so forth. It has a maximum speed of 300 km/h and will connect Taipei and Kaohsiung (345 km) in as little as 1.5 hours. While TSC has received orders beyond rolling stock for signaling systems, track, and so forth, Kawasaki was the primary contracting company for rolling stock and has manufactured 30 trains (360 cars) together with Nippon Sharyo Ltd. and Hitachi Ltd.
2005
Kawasaki Plant Systems, Ltd. (K Plant) is established as a wholly owned subsidiary.
2006
Kawasaki Environmental Engineering, Ltd. (KEE) is established as a wholly owned subsidiray.
2007
K Plant and KEE merge to form new K Plant.
2007
Rolls out test planes for the XP-1 fixed-wing maritime patrol aircraft and XC-2 transport aircraft
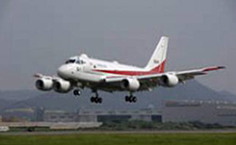
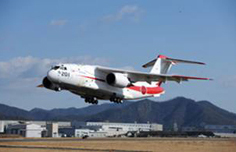
In 2007, test planes for fixed-wing maritime patrol aircraft (XP-1) and transport aircraft (XC-2) were rolled out at its Gifu Works. In 2001 Kawasaki had been designated the primary contractor for the XP-1 and XC-2 by the Ministry of Defense. The project to develop the XP-1 and XC-2, initiated by the Ministry of Defense in 2001, was the first domestic program to develop large-size aircraft since the C-1 forty years earlier, and the first-ever Japanese effort to work on two such aircraft simultaneously. Following testing of both aircraft at the Gifu Works, Kawasaki delivered the XP-1 to the Ministry of Defense in 2008, and the XC-2 in 2010.
2009
KCM Corporation is established as a wholly owned subsidiary.
2010
Kawasaki Shipbuilding Corporation, Kawasaki Precision Machinery Limited (KPM) and Kawasaki Plant Systems, Ltd. (K Plant) are re-merged into Kawasaki Heavy Industries, Ltd.
2013
Established Medicaroid Corporation, a marketing company for the development of medical robots, jointly with SYSMEX CORPORATION.
2015
All KCM Corporation shares transferred to the Hitachi Construction Machinery Group.
2017
Completes first US production line for cargo doors for Boeing’s commercial airplanes
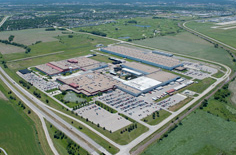
In 2017, Kawasaki opened a production line to manufacture cargo doors for Boeing’s state-of-the-art commercial airplane, the 777X, at the Lincoln Plant of Kawasaki Motors Manufacturing Corp., U.S.A. (KMM), located in the state of Nebraska. Since December 2015, the company had been building the line in the approximately 2,800 m2 work area in the Plant’s existing building, and it now also features Kawasaki’s first aerostructures production line in the U.S. The line includes various types of cutting-edge equipment and systems to advance facility automation, thereby achieving high-quality, high-efficiency production. This equipment includes Kawasaki robots capable of precise, detailed painting operations, and auto riveters with an expanded operating range.
2018
Kawasaki's US plant completes first commercial aircraft cargo doors for Boeing

In September 2018, at the Lincoln Plant, Kawasaki manufactured its first cargo doors for Boeing’s commercial aircraft. The aerostructures production line at the Plant features various types of cutting-edge equipment and systems to advance facility automation, including Kawasaki robots capable of precise, detailed painting operations, and auto riveters with an expanded operating range. The plant also incorporates into line operations the unique Kawasaki Production System (KPS), developed through mass-production activities over the years, to achieve high-quality, high-efficiency production, while utilizing U.S.-made, locally procured materials and parts to cut down on transportation costs and reduce lead times.
2021
Kawasaki Railcar Manufacturing Co., Ltd. and Kawasaki Motors, Ltd. are established as wholly owned subsidiaries.