Cement Plant
History
Kawasaki Heavy Industries, Ltd. has supplied a lot of cement manufacturing equipment worldwide since its first delivery of a rotary kiln in 1932. The cement plant we designed and constructed has attracted the attention of the world's cement manufacturers and specialists due to its advanced performance. Kawasaki’s large-scale and energy-saving cement plants have so far been supplied around the world and admired by users for the stable running performance.
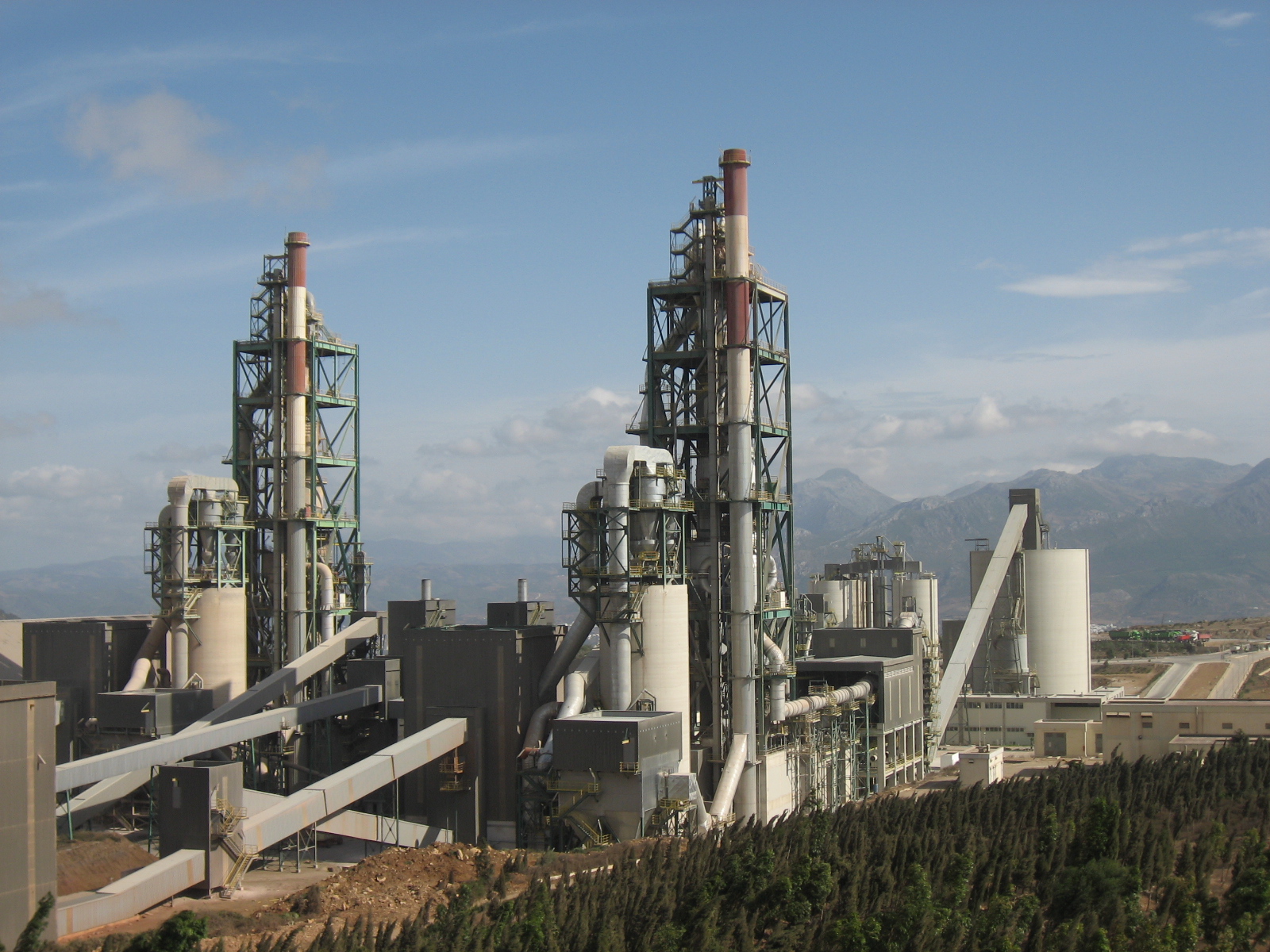
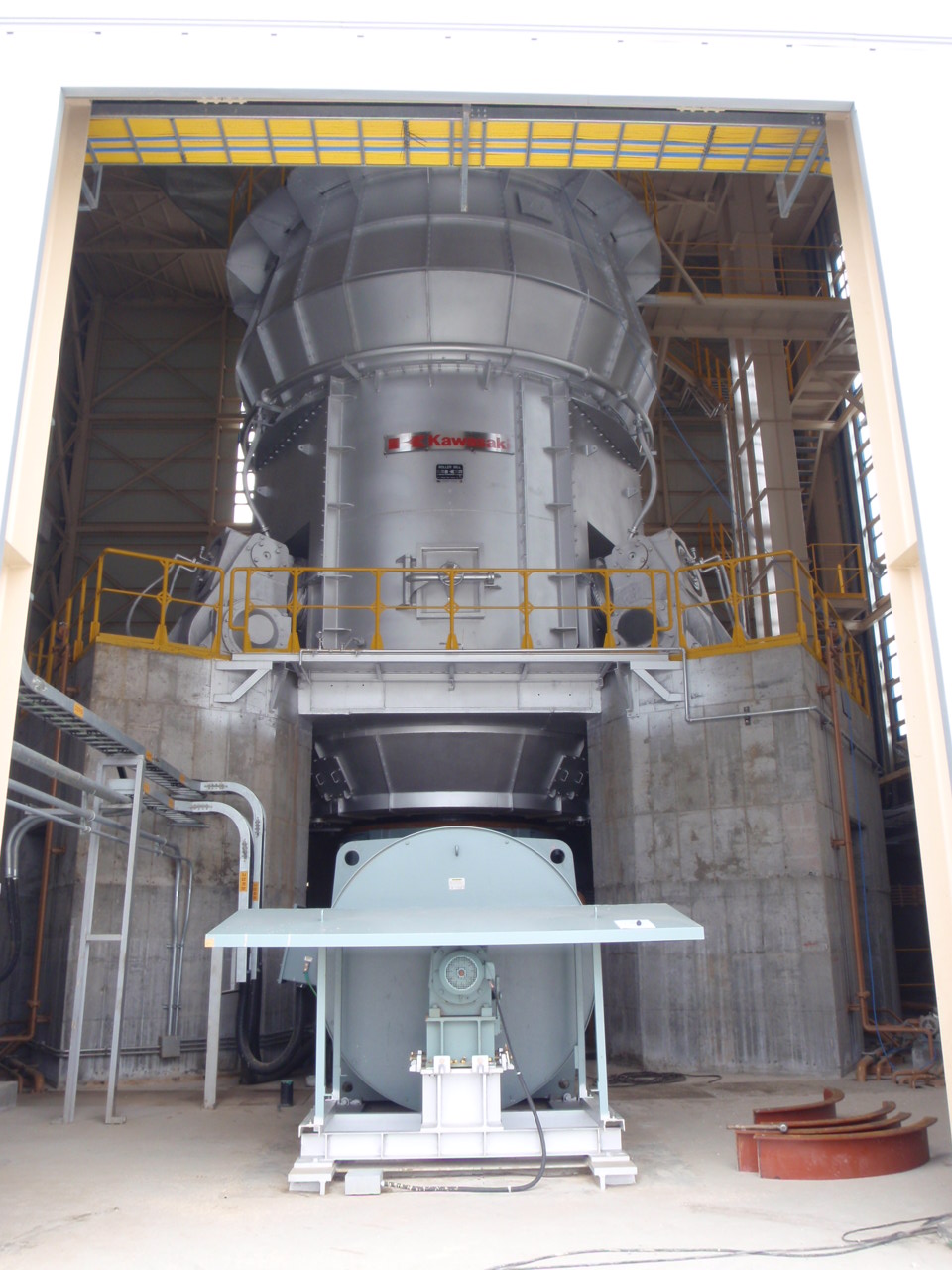
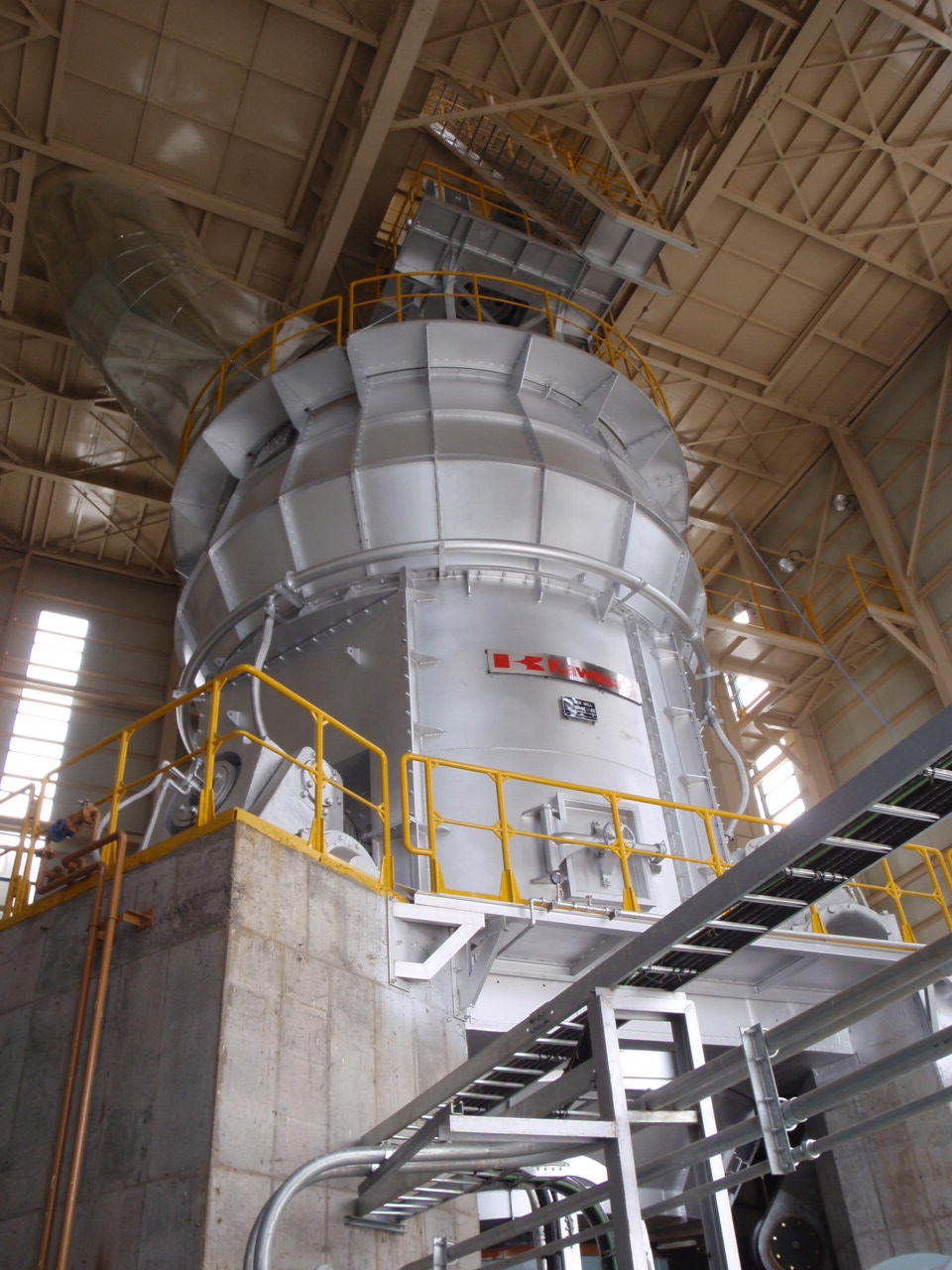
Strength in Total Solution
Our strength lies in our comprehensive technologies including the feasibility study, designing, manufacturing, procurement, construction, commissioning, operation & maintenance, renovation of cement plants as well as manufacturing machinery for cement plants. We have also applied these technologies to the nonferrous metals processing plant and limestone calcining system. Each system has achieved remarkable results in energy saving and high efficiency.
New Approach
Following Kawasaki's engineering center in Philippines (KDT), Kawasaki has established three joint companies, ACK, CKM and CKE in China for engineering, procurement and manufacturing of cement plant equipment. Kawasaki can provide high-performance equipment developed by our prominent technologies to suit investment needs of customers. Kawasaki has taken over cement plant business of IHI Corporation, and furthermore acquired OK Vertical Roller Mill technologies.
Eco-friendly Development
The cement machinery and equipment manufactured by Kawasaki leads to superior performance of energy saving, high efficiency and environmental protection. Kawasaki "Low-NOx" KSV (Kawasaki Spouted Bed & Vortex Chamber) and In-Line Precalciners have been delivered to major cement companies and contributed denitration and energy saving. As of September 2024, 75 units of KSV, ranging 1,000 to 12,000 tons per day have been delivered. Kawasaki's new generation CK Mills are highly valued for the low power consumption. Kawasaki has secured and/or delivered 156 units of the CK Mills since launching.
Cement Waste Heat Recovery Plant
We can provide plants with much higher energy efficiency in response to customers' environment-friendliness by combining our Waste Heat Recovery Power Generation System. This system utilizes the thermal energy of the exhaust gas from SP (NSP) and clinker cooler, and thus generates and covers 30%-40% of electric consumption in a cement plant. Kawasaki is a pioneer in waste heat recovery technologies.
Zero Emission Eco Town (ZEET) System
The Zero Emission Eco Town (ZEET) System is an integrated system of cement plant and incineration plant. The ZEET System treats refuse and sludge hygienically, and processes into energy and raw materials for cement manufacturing. This system reduces the fuel consumption for cement manufacturing by obtaining energy from gasified refuse. Since the burned ash is used as raw materials for cement, the final disposal of the ash is no longer required. This system reduces CO2 emissions as compared to disposal by landfill.
Features
In addition to total engineering, we manufacture raw mills, kilns, and cement mills which are integral to the quality and energy saving in cement manufacturing.
1) Kiln Product Line
-New Suspension Pre-heater
-Rotary Kiln / Rotary Dryer
2) Mill Product Line
-Tube Mill & Separator
-CK Roller Mill
-CKP Roller Mill
Major Delivery
1997 Indonesia / PT Indocement Tunggal Prakarsa P-10 (3,800tons/day)
1999 Indonesia / PT Indocement Tunggal Prakarsa P-11 (7,500tons/day)
2002 Myanmar / Myanmar Economic Corporation (4,000tons/day)
2003 U.A.E. / Sharjah (3,400tons/day)
2003 Vietnam / VNCC Bimson (3,500tons/day)
2004 Morocco / Lafarge Ciments (2,300tons/day)
2004 Morocco / Holcim (Cement Mill 115tons/hour)
2005 Turkmenistan / GAP Insaat Yatirim Ve Dis Ticaret A.S. (3,000tons/day)
2008 Vietnam / Vietnam Construction Import-Export Corporation (VINACONEX) (6,000tons/day)
2009 Yemen / "Yemen General Corporation for Cement Industry & Marketing" (3,300tons/day)
2009 Morocco / Lafarge Ciments (2,300tons/day, Expansion project)
2010 Vietnam / VNCC Butson Cement Company (4,000tons/day)
2010 Vietnam / Bimson Cement Joint Stock Company (5,500tons/day)
Contact
If you need more information about our business,
please feel free to contact us.