CO2 FREE (Realization of a Carbon-neutral Society)
In October 2020, the Japanese government declared its target of achieving carbon neutrality by 2050, to this end raising its fiscal 2030 reduction target for CO2 emissions from 26% to 46% (both compared with the fiscal 2013 level) in April 2021. This is but one example of decisions made by countries around the globe amid the accelerating trend toward across-the-board decarbonization and the realization of a low-carbon society. Toward achieving the CO2-free target set out in the Kawasaki Global Environmental Vision 2050, the Kawasaki Group is not only actively engaged in realizing carbon neutrality at its plants (Scope 1 and 2) but also throughout its supply chain (Scope 3).
- Carbon Neutrality Targets (Medium- to Long-term Targets)
- Information Disclosure in Line with the TCFD Recommendations (Scenario Analysis)
- Environmental Management Activities Plan 2024 (Short-term Target and Plan)
- External Affairs Activities Concerning Climate Change
Carbon Neutrality Targets (Medium- to Long-term Targets)
In August 2024, Kawasaki received certification of its greenhouse gas reduction targets from the Science Based Targets initiative (SBTi*1), an international climate change initiative. The certified targets include two types based on fiscal 2022: a short-term target (NEAR-TERM) and a long-term target (NET-ZERO). The short-term target aims to reduce Scope 1 and 2 emissions by 50.4% compared to fiscal 2022 by fiscal 2032, and Scope 3 Category (xi) emissions by 30% compared to fiscal 2022. The long-term target aims to achieve net-zero greenhouse gas missions across the entire value chain by fiscal 2049. The Group has set its own CO2 mission reduction targets in advance of obtaining SBT certification. In particular, for Scope 1 and 2, we have established ambitious targets that exceed SBT certification standards. Through voluntary initiatives centered on hydrogen power generation, we aim to achieve net zero domestically by 2030. To address Scope 3 emissions, we will decarbonize products and services with hydrogenation, electrification, green power grid, alternative fuels, and CCUS*2 as our keywords and strive to achieve by 2040 a status where customers select our Zero-Carbon Ready decarbonization solutions. The target for Scope 3 Category (xi), already SBT-certified, is positioned as an intermediate goal for 2040. Ultimately, we aim to achieve net zero across our entire value chain by 2050, in line with the long-term goals of SBT certification. We will expand our decarbonization solutions together with our business partners and customers, contributing to the early realization of carbon neutrality.
- *1 SBTi: An international initiative jointly established in 2015 by CDP, the United Nations Global Compact, the World Resources Institute (WRI), and the World Wide Fund for Nature (WWF). It defines and promotes best practices for science-based target setting and independently evaluates corporate targets.
- *2 CCUS (Carbon dioxide Capture, Utilization and Storage): Capture CO2 emissions + Store underground + Utilize CO2
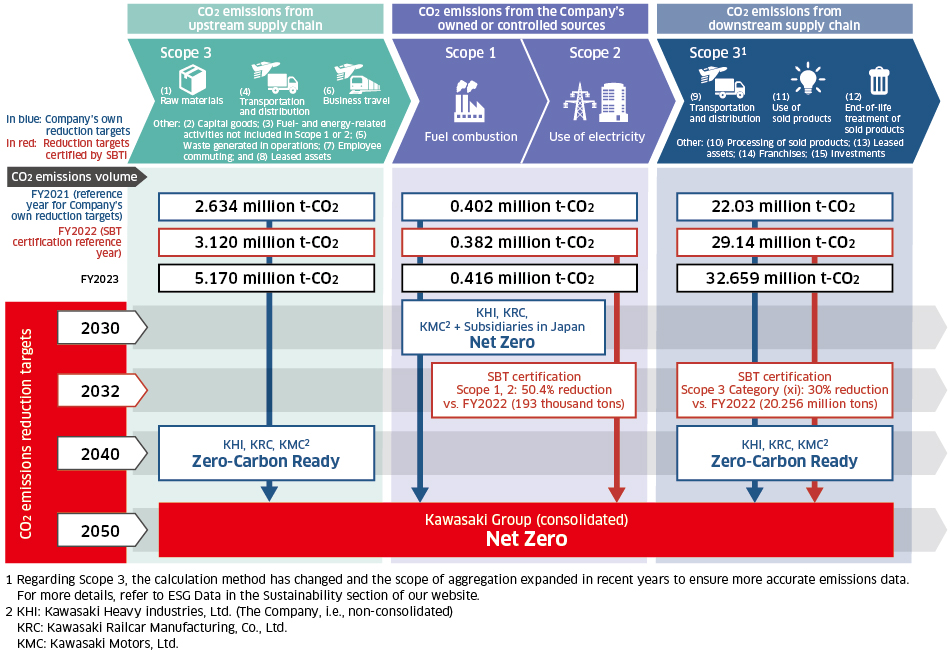
Scope 1 and 2
Corresponding companies: Kawasaki Heavy Industries, Kawasaki Railcar Manufacturing, Kawasaki Motors + Affiliated companies in Japan
Toward the Realization of Independent Carbon Neutrality by 2030 through Initiatives Focusing on Hydrogen Power Generation
As shown to the right, the Kawasaki Group’s Scope 1 and 2 CO2 emissions are approximately 400,000 tons annually, of which Japan account for three-quarters. We will continue efforts to save even more energy and promote electrification and the use of sustainable energy, such as solar power generation, to reduce CO2 emissions through 2030. We will also introduce in-house hydrogen-fueled power generation facilities and achieve zero-emissions plants by combining this with power generation from waste, renewable energy, and other energy sources. Through these initiatives, we plan to achieve independent carbon neutrality with zero CO2 emissions by the Group in Japan by 2030. We are also working to reduce CO2 emissions overseas.
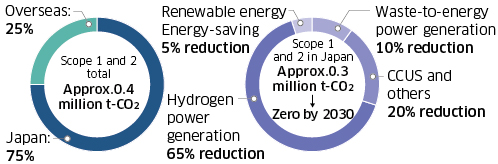
Zero-Emissions Plant
Zero-emissions plant refers to initiatives to achieve zero CO2 emissions from plants by obtaining the electricity and thermal energy used at the plants from a combination of methods that do not emit any CO2, such as hydrogen power generation, solar power generation, and waste power generation. The Kawasaki Group will reduce CO2 emissions throughout the Group by converting its plants in Japan to zero-emissions plants by 2030.
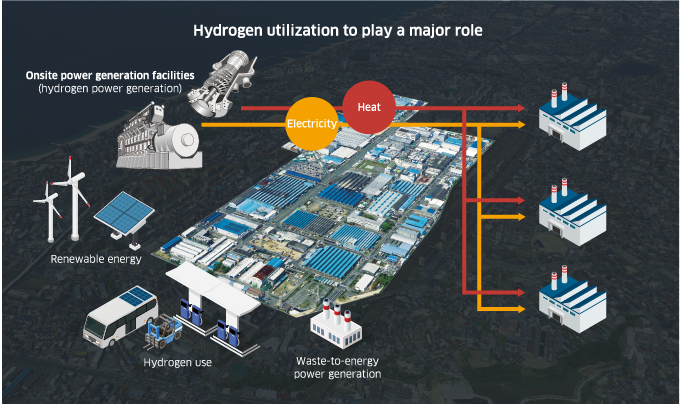
Scope 3
Corresponding companies: Kawasaki Heavy Industries, Kawasaki Railcar Manufacturing, Kawasaki Motors
Leading Society by Advancing Toward Zero-Carbon Ready
Scope 3 Net Zero can only be achieved when all parties in the value chain including trading partners and clients become Zero-Carbon Ready. The Company will implement the maximum possible measures concerning Scope 3 to become Zero-Carbon Ready by 2040. Specifically, for category (i), we will slash CO2 emissions by suppliers of materials and parts by 80% compared to fiscal 2021, and for category (xi), we will develop a lineup of CO2-free standard solutions in all businesses. Moreover, we will reduce CO2 emissions by more than the Company’s own Scope 3 emissions by working toward achieving a hydrogen-based society and engaging in the CCUS business, thereby contributing to the early achievement of carbon neutrality around the world.
Scope 3 Breakdown by Categories
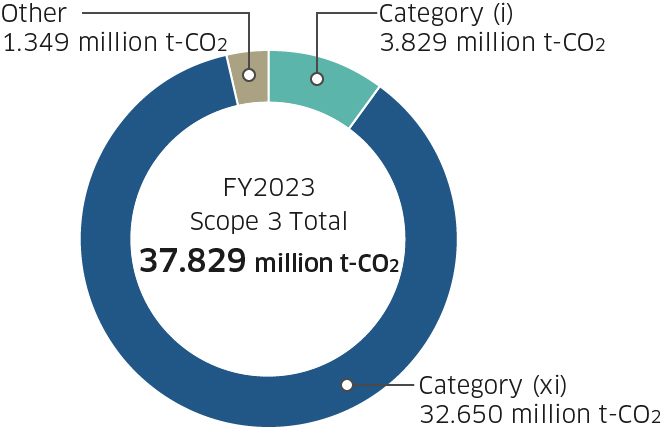
* Regarding Category (xi) in Scope 3, from fiscal 2022, the scope of calculation was expanded from a total of KHI, KRM, and KMC, to the Kawasaki Group.
Scope 3 Category (i) Procurement of materials and parts
Support industrial initiatives with hydrogen and CCUS solutions to further accelerate reductions
It is anticipated that many industries and companies will tackle the reduction of CO2 emissions through various measures, including the utilization of renewables and efficient energy use. The Company will deepen its partnerships, including sharing emissions data with business partners, offering support for CO2 reductions and striving for early achievement of zero emissions. This will be achieved by means not limited to in-company utilization by the Group of solutions such as hydrogen power, hydrogen fuel, and other alternative fuels, as well as CCUS, but also by providing these solutions to business partners that supply materials and parts. As a first step, in fiscal 2023, we introduced tools for visualizing CO2 emissions from procurement in some businesses and conducted briefings and study sessions on carbon neutrality for business partners. Furthermore, in April 2024, we held a briefing on carbon neutrality for our main business partners to provide an overview of the Kawasaki Group’s initiatives and guidelines toward the realization of a carbon-neutral society. Meanwhile, we are also promoting collaboration with our suppliers, such as making requests that they undertake initiatives to reduce their CO2 emissions.
Scope 3 Category (i) (CO2 reductions scenarios)
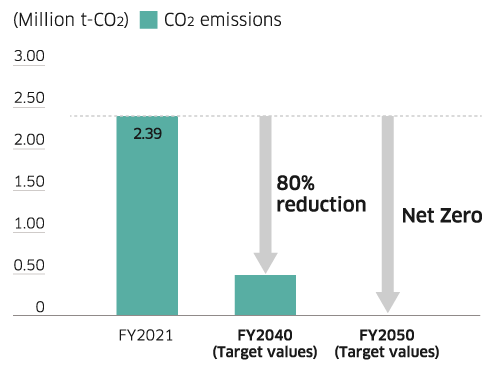
Scope 3 Category (xi) Providing customer solutions
Provide CO2-free solutions to all customers
We will take action to decarbonize products and services with hydrogenation, electrification, green power grids, alternative fuels, and CCUS as our keywords. In the short-term initiatives toward 2030, through Kawasaki Ecological Frontiers, a program for certification of environmentally friendly products, and other initiatives, we will continue to reduce the energy consumption and improve the efficiency of existing products and promote the shift to hybrid electric and battery electric motorcycles and other vehicles as part of the transition to a decarbonized society. We will also conduct development for the commercialization of hydrogen energy and expand the use of hydrogen in gas turbines, gas engines, and other equipment. Furthermore, we will work toward the development of Kawasaki CO2 Capture and DAC for the capture and use of CO2. In medium- to long-term initiatives toward 2040, the Group will actively further the following three major initiatives. The first will be the provision of CO2-free fuels and electrical power to society, with a focus on its hydrogen business. The second will be to make a selection of choices for electrification and CO2-free fuels available to customers utilizing our various solutions including mobility and robots. The third will be promoting CO2 capture as well as the effective use of CO2 including the manufacture of synthetic fuels and chemical products to achieve a circular CO2 society. With these three pillars, the Group will make choices available to our customers of products and services (excluding defense and related; emergency products business) that contribute to the achievement of carbon neutrality by 2040, and promote global reductions in CO2.
* From fiscal 2021, the Group modified its calculation method to allow more accurate records of emissions levels for Scope3 category (xi). Previously, CO2 emissions levels for products such as hydraulic machinery, manufactured as parts to be incorporated in finished products, were calculated by tallying the CO2 emissions levels of the finished products such as construction machinery. However, from fiscal 2021, these calculations will also take into account the degree of contributions and weight ratios for final products.
Decarbonization Solution Initiatives by Business
In all businesses, we provide decarbonization solutions through a shift to hydrogen, electrification and green power grids, and CCUS/alternative fuels. We seek to carry out optimal decarbonization transitions in each business, provide CO2-free solutions, and reduce CO2 throughout society while expanding the scale of our business.
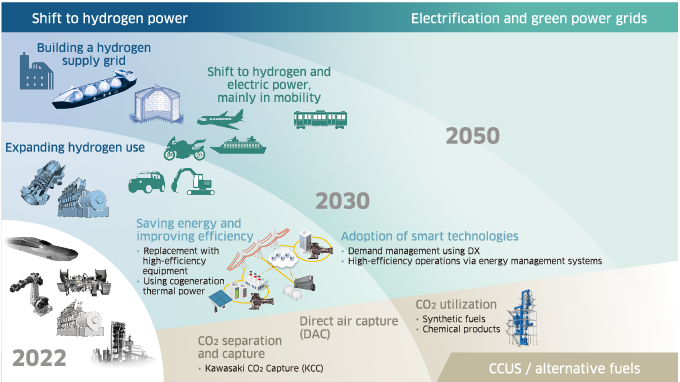
Direction of Transitions by Business
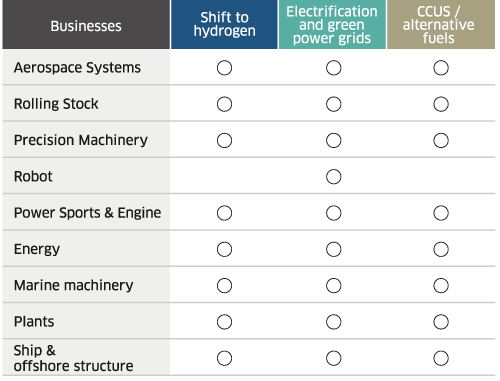
Envisioned Scale of Business by Future Solution
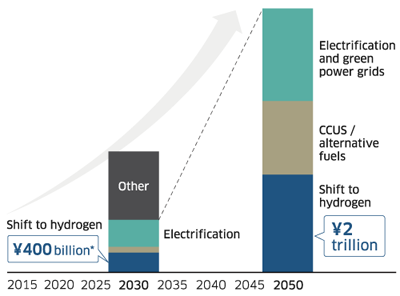
* Following Group Vision 2030・Business Report Meeting held on December 6, 2022, the net sales target was revised from 300 billion yen to 400 billion yen.
Measures for the Effective Use of CO2 to Achieve a Circular CO2 Society
We will not simply store the CO2 that we recover at KCC and DAC, but will also work toward achieving a circular CO2 society by means such as the effective use of CO2 including the manufacture of synthetic fuels and chemical products through synthesis with CO2-free hydrogen.
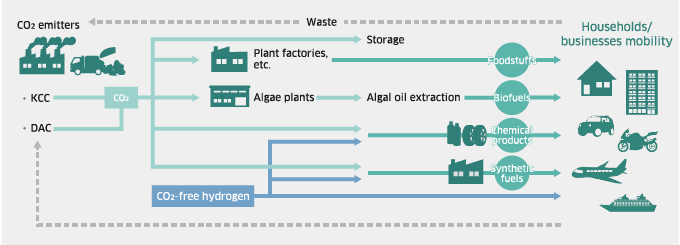
Information Disclosure in Line with the TCFD Recommendations (Scenario Analysis)
Climate change-related information based on TCFD recommendations is reported in the Kawasaki Report. Please refer to the link below for the details on our report after fiscal 2023.
Environmental Management Activities Plan 2024 (Short-term Target and Plan)
Aiming to achieve its carbon neutrality target (medium- to long-term target), in the short-term, while the Company will step up efforts to introduce in-house hydrogen power generation by 2030 to achieve carbon neutrality at its plants (Scope 1 and 2), it will continue its ongoing efforts to scale the introduction of renewable energy and to save energy. Furthermore, the Company will accelerate these efforts with the introduction of internal carbon pricing. To achieve carbon neutrality in its supply chain (Scope 3), the Company aims to realize Zero-Carbon Ready by 2040 by advancing its provision of CO2-free solutions to its business partners and customers. One aspect of Scope 3 reductions is the public disclosure of CO2 emissions reduction contributions* by products.
* For information on emissions reduction contributions, refer to “Reducing CO2 Emissions through Product-Based Contributions” below on this page.
The Environmental Management Activities Plan 2023 (Key Strategies) and Achievements in Fiscal 2023
Key Strategies of the Environmental Plan 2023 | Achievements in Fiscal 2023 |
---|---|
(a) Reduction of CO2 emissions in entire supply chain | |
|
|
|
|
|
|
|
|
|
|
(b) Expanded introduction of decarbonized energy | |
|
|
|
|
(c) Promotion of energy-saving activities | |
|
|
(d) Fuel conversion | |
|
|
The Environmental Management Activities Plan 2024 (Key Strategies)
Key Strategies of the Environmental Plan 2024 |
---|
(a) Reduction of CO2 emissions in entire supply chain
|
(b) Expanded introduction of decarbonized energy
|
(c) Fuel conversion
|
Scope 1 and 2 Efforts
Corresponding companies: Kawasaki Heavy Industries, Kawasaki Railcar Manufacturing, Kawasaki Motors
Utilizing Renewable Energy
The Kawasaki Group is advancing the use of renewable energy to reduce the CO2 emissions from its plants. To this end, we are installing solar power generating systems at our plants. We have a total solar power generation capacity of 12,610 kW including Group companies. In fiscal 2023, these systems generated 13,632 MWh, of which 10,488 MWh was used in-house. Electric power used in-house is equivalent to 1.51% of the electricity consumed throughout the entire Group.
The Kawasaki Group’s Solar Power Generation Capacity
Name | Power Usage | Generation Capacity (kW) |
---|---|---|
Iwaoka Photovoltaic Power Generation Station1*1 | Sold via FIT*2 | 1,505 |
Nagoya Works 1 | Used in-house | 750 |
Seishin Works | Used in-house via PPA | 1,444 |
Seishin Photovoltaic Power Generation Station*1 | Sold via FIT | 701 |
Nishi-Kobe Works | Used in-house | 627 |
Nishi-Kobe Photovoltaic Power Generation Station*1 | Sold via FIT | 422 |
Akashi Works | Used in-house | 230 |
Sakaide Works | Used in-house | 50 |
Kakogawa Photovoltaic Power Generation Station*1 | Sold via FIT | 48 |
Kobe Head Office of Kawasaki Railcar Manufacturing Co., Ltd. | Used in-house | 25 |
Kobe Works | Used in-house | 20 |
Kawasaki Thermal Engineering Co., Ltd. | Used in-house | 7 |
Harima Works | Used in-house via PPA | 783 |
Kawasaki Motors Enterprise (Thailand) Co., Ltd. | Used in-house via PPA | 5,000 |
Kawasaki Precision Machinery (UK) Ltd. | Used in-house | 999 |
Total | 12,610 |
- *1 Power generation facility operated by Kawasaki Trading Co., Ltd.
- *2 FIT: Feed-in tariff; a program in which renewable energy is bought back at a fixed rate
Photovoltaic output (including power sold via FIT)
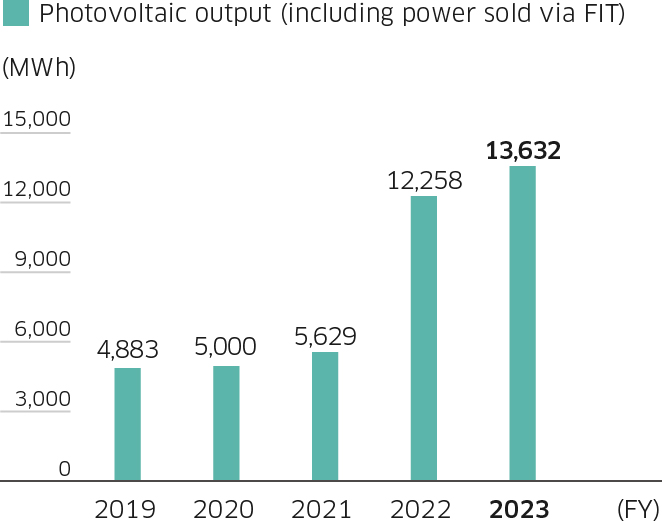
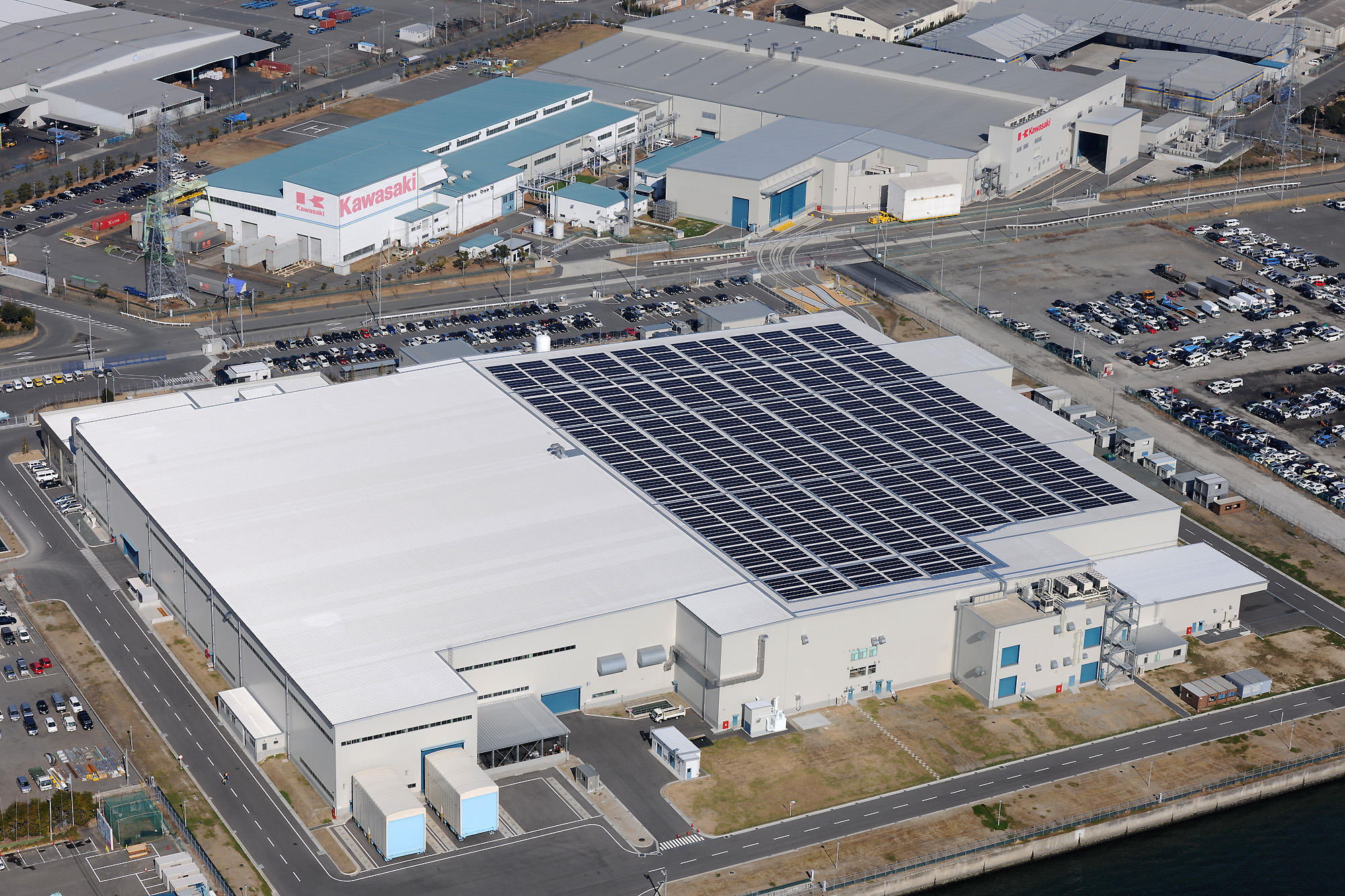
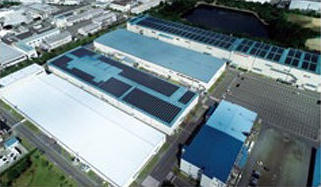
Systematic Investment in Energy-Saving Equipment
As a measure to promote energy-saving activities, in 2022, the Company introduced an initiative to set reference values for the CO2 reduction efficiency of energy-saving investment projects as criteria for determining the investment in such projects and to increase the equipment budget allocation for projects in which the reduction efficiency meets the criteria. Through this initiative, the Company will continue to reduce its CO2 emissions by advancing its investments in equipment with a focus on projects with a high CO2 reduction efficiency. Such equipment investment projects include upgrading production equipment, switching air conditioning systems to those that run on electricity, and changing to LED lighting. In addition, in accordance with the Act on Rationalization of Energy Use and Shift to Non-fossil Energy, Kawasaki Heavy Industries, Kawasaki Railcar Manufacturing, and Kawasaki Motors aim to reduce unit energy consumption by an average of 1% per year.
Internal Carbon Pricing
To promote investment in carbon neutrality efforts such as the introduction of future hydrogen equipment and renewable energy and to change behavior within the Company, since fiscal 2022, the Company has introduced internal carbon pricing. Specifically, a carbon surcharge will be imposed in an amount calculated by multiplying the Scope 1 and 2 emissions of Kawasaki Heavy Industries, Kawasaki Railcar Manufacturing, and Kawasaki Motors in the previous fiscal year by a CO2 unit price (2000 yen/t-CO2). The aim is to make concentrated investments in carbon neutrality efforts based on the funds generated from surcharges of the internal carbon pricing program.
Reducing CO2 Emissions through Product-Based Contributions
Corresponding companies: Kawasaki Heavy Industries, Kawasaki Railcar Manufacturing, Kawasaki Motors
Nearly 90% of CO2 emitted during the life cycles of our products is released during the period of their use after they are sold. Therefore, the Company seeks to realize a carbon-neutral society by providing products that produce only low CO2 emissions during their use. To reduce products’ post-sale CO2 emissions, in addition to increasing product energy efficiency, we are advancing electrification and modal shifts when replacing existing products in our product lineup and expanding our lineup of products that utilize exhaust heat, waste, and renewable energy. Key products that help reduce CO2 emissions are listed below. In fiscal 2017, we revised our rules for calculating CO2 emissions reductions through product-based contributions in order to better quantify the contributions of such products to the mitigation of global warming. Calculations based on these rules showed that the CO2 emissions reduction* through products we sold in fiscal 2023 was about 16.30 million tons. Large contributions were made mainly by the M7A Series gas turbines for power generation, which boast excellent reliability, economy, and environmental friendliness and are certified under the Kawasaki Ecological Frontiers system, an internal certification program for environmentally conscious products, and the KC-MB-20, a controller for use in construction machinery to improve its fuel efficiency via the application of superior controlling technologies.
* Reduction in CO2 emissions compared to earlier products (refer to the calculation rules below.)
Key Products That Contribute to Reducing CO2 Emissions During Use (by Segment)
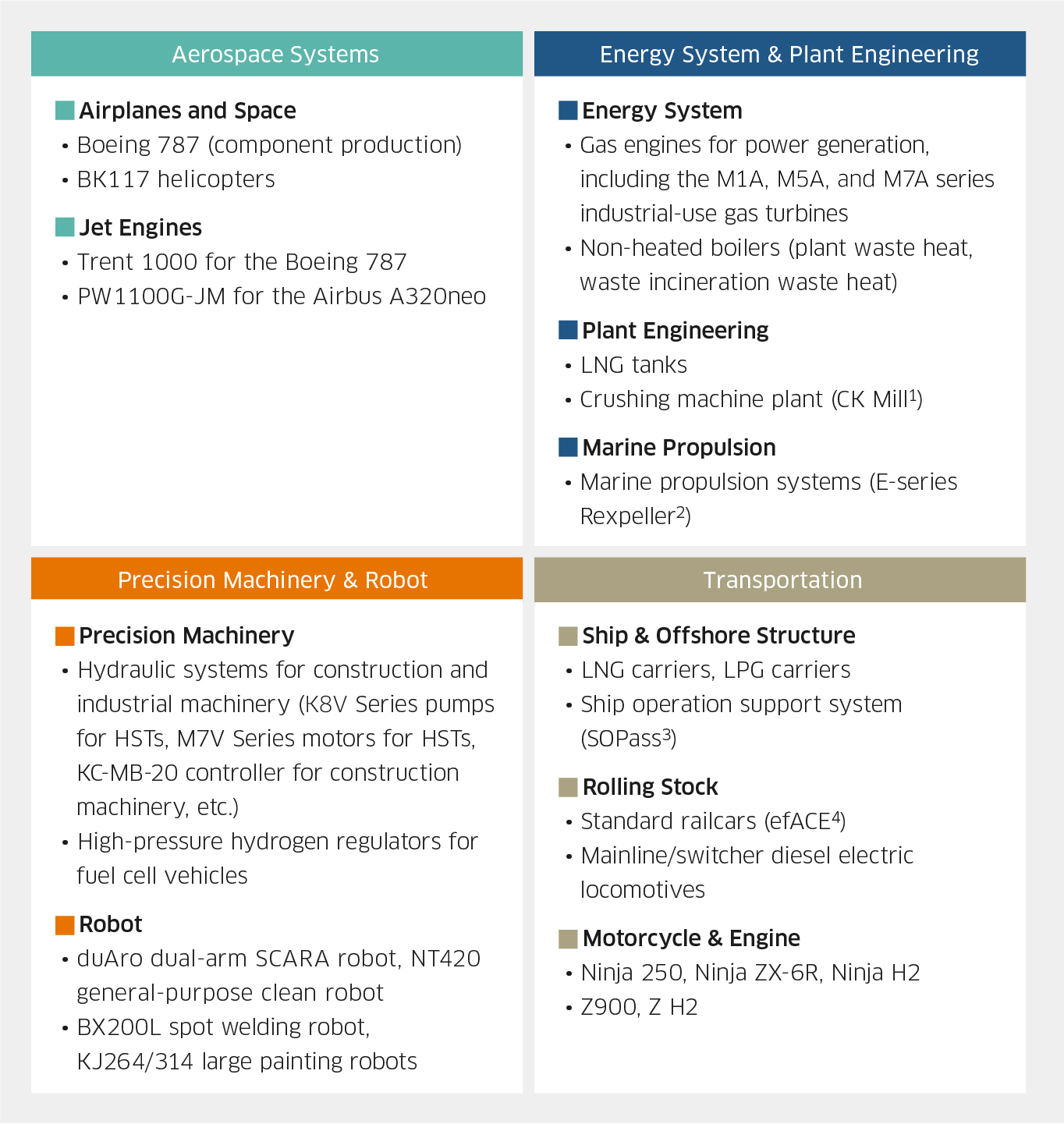
- *1 CK Mill: Named after the companies that jointly developed it, Chichibu Cement Co., Ltd. (now Taiheiyo Cement Corporation) and Kawasaki.
- *2 Developed with a focus on three Es: energy saving, easy maintenance, and environmentally friendly.
- *3 Ship Operation and Performance analysis support system
- *4 Environmentally Friendly Advanced Commuter & Express train
Calculation Rules
- Products to be assessed: Kawasaki Ecological Frontiers system, products that use waste, waste heat, and renewable energy, as well as cogeneration systems and rolling stock pertaining to modal shifts, etc., were selected for assessment
- Period of assessment: Until fiscal 2016, we used a one-year period of assessment. However, in line with the revision of the calculation rules, since fiscal 2017, we have adopted a flow-based approach* in which the period of assessment is the estimated useful life of products sold in the fiscal year, because the estimated useful lives of our products are long. This allows us to better calculate the difference in CO2 emissions between our products and industry standard class products over the entire period of use.
- The calculation method expressed as a calculation formula is as follows: CO2 emissions through product-based contributions = (annual CO2 emissions from conventional products - annual CO2 emissions from new products) x (assumed number of usage years)
* Please refer to the "Guideline for Quantifying Greenhouse Gas Emission Reduction Contribution" (Ministry of Economy, Trade and Industry, March 2018)
In order to quantify the contributions of highly energy efficient products to the mitigation of global warming, products included in the calculation of CO2 emissions reduction through product-based contributions include power generated through waste heat, waste, renewable energy, and so forth. As a result, some of the products included differ from those included in the calculation of Scope 3, category (xi), which covers only energy-derived CO2 emissions. CO2 emission reductions for the past five years are shown in the graph below. Particularly notable products that have had a large cumulative effect are shown below.
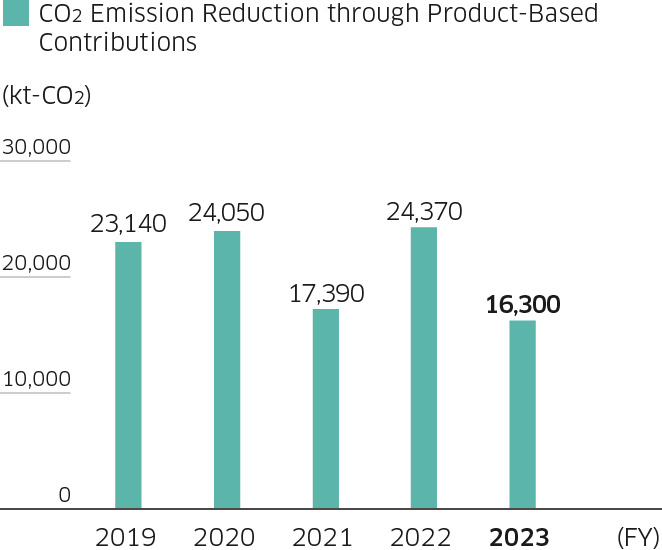
- Notes: 1. Kawasaki uses CO2 emissions factors provided in the list of calculation methods and emissions factors published by Japan’s Ministry of the Environment.
- 2. The CO2 emission reduction effect through product-based contributions achieved through the higher energy efficiency of products is based on a comparison using industry standard products.
- 3. The application of waste heat, waste, and renewable energy is counted toward the CO2 emissions reduction effect through product-based contributions.
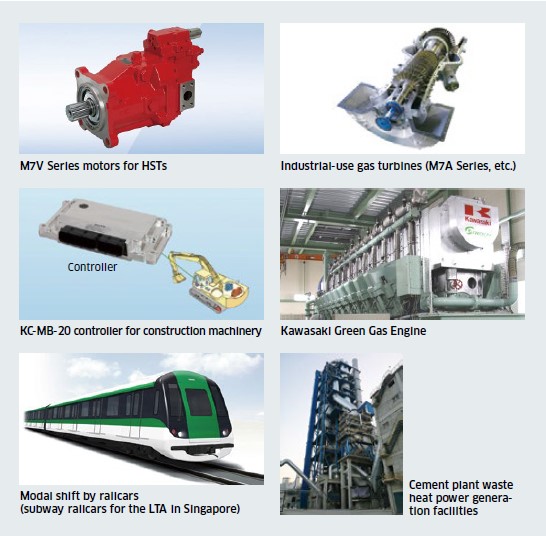
For details on the Kawasaki Ecological Frontiers certification system for environmentally conscious products, please refer to environmentally conscious products.
External Affairs Activities Concerning Climate Change
Our Basic Stance and Structure
To contribute to realization of a society that limits the increase in the global average temperature to 1.5°C compared to pre-industrial times, the objective of the Paris Agreement, the Kawasaki Group is using its technological knowledge and expertise relating to decarbonization, actively participating in trade association activities, and contributing to the formulation of policy recommendations concerning climate change mitigation and adaptation. The directors in charge of the relevant departments ensure that trade association and public policy engagement is in line with the Group’s strategies concerning responses to climate change and report as necessary to the Board of Directors, the highest decision-making body responsible for deliberating on and finalizing fundamental sustainability policies and basic plans for the entire Group. In cases where we identify substantial misalignments between the activities of organizations of which the Group is a member and the objectives of the Paris Agreement, we engage in constructive dialogue with those organizations based on the Group’s climate change strategy and business activities, and if those misalignments cannot be eliminated after the passage of a certain period of time, we consider appropriate responses including withdrawal.
Engagement in Public Policy and Regulations Concerning Climate Change
Hydrogen, a source of clean energy that does not emit any CO2 during use, has become a focus of attention as one solution for achieving a carbon neutral society by 2050. In response, the Kawasaki Group has positioned the achievement of carbon neutrality centered on hydrogen electricity generation as one pillar of our climate change strategy and is now working to carry out that strategy in collaboration with policymakers and trade associations. Group Vision 2030, our management strategy, positions new business including the hydrogen business as our primary growth scenario and seeks to achieve the 1.5°C target in line with the Paris Agreement. The hydrogen business in particular is positioned at the center of the Company’s business growth and transition plan, and we are actively cooperating with policymakers, trade associations, and others to assess hydrogen GHG emissions and formulate international supply chain rules with the aim of achieving the objectives of Group Vision 2030 and carbon neutrality at an early stage.
Participation in the Development of the Methodology to Assess GHG Emissions of Hydrogen at IPHE
In order to promote low-carbon hydrogen utilization in society toward the realization of a carbon-neutral society, it is necessary to evaluate the hydrogen to show that it is low-carbon, and it is ideal that the evaluation criteria are standardized internationally. The methodology for determining greenhouse gas (GHG) emissions of hydrogen is discussed in IPHE (International Partnership for Hydrogen and Fuel Cells in the Economy), an international inter-governmental partnership whose objective is to facilitate and accelerate the transition to clean and efficient energy and mobility systems using fuel cells and hydrogen technologies. Our company has participated in this discussion as an expert supporting the Ministry of Economy, Trade and Industry, Japanese government, and has made a significant contribution, including providing technical advice, particularly about liquefied hydrogen supply chain.
|
Establishing International Rules Relating to Assessment of CO2 Emissions in Hydrogen Supply Chains
The Kawasaki Group is using the technical knowledge and data concerning international liquefied hydrogen supply chains that it has accumulated as a top runner in an effort to establish international rules relating to methodology for calculating CO2 emissions in collaboration with relevant organizations. Specifically, in May 2023, we announced a collaboration with DNV, an international third-party certification body, to establish methods of calculating CO2 emissions during maritime transportation of liquefied hydrogen. Our ultimate objective is to have our efforts reflected in standardized international rules. We also participated in the formulation of the Technical Specification relating to a methodology for calculating CO2 emissions in processes from hydrogen production to transport issued by the ISO in November 2023. In addition, Yoshinori Kanehana, the Company’s Chairman of the Board, served as co-chair of the Hydrogen Council from January 2022 to June 2024. The Hydrogen Council is an organization that promotes the roles that hydrogen can play in the global-scale transition to alternative fuels and currently has approximately 140 members from various industries around the world. We participate in discussions on methodologies for evaluating GHG emissions with council members.
|
Active Contribution to Climate Change Organization
HySTRA
As a member of HySTRA (CO2-free Hydrogen Energy Supply-chain Technology Research Association), the Company participates in efforts to build a CO2-free hydrogen supply chain consisting of hydrogen production, transport/storage, and utilization, and works to establish and verify the relevant technologies to be commercialized by around 2030. The Company's role at HySTRA is to engage in building liquefied hydrogen carriers and constructing liquefied hydrogen unloading equipment and bulk storage facilities by utilizing the cryogenic technologies it has developed such as for LNG carriers, LNG storage tanks, and liquefied hydrogen tanks for rocket fuel.
JH2A
The Company has participated in the Japan Hydrogen Association (JH2A), an organization that promotes global collaboration on the hydrogen field and the formation of hydrogen supply chains, as an executive board member since its foundation in December 2020. We support the purpose of the JH2A, which is to build a hydrogen society at an early stage through the realization of social implementation projects, and by working with other member companies and organizations, national and local governments, and academia, we are promoting the “global collaboration and cross-industry, open initiatives in the hydrogen field” supported by the JH2A, thereby contributing to the development of hydrogen supply chains and a hydrogen society.
|
Contact
If you need more information about our business,
please feel free to contact us.