LNG Carrier Grace Dahlia Delivered
Sep. 30, 2013
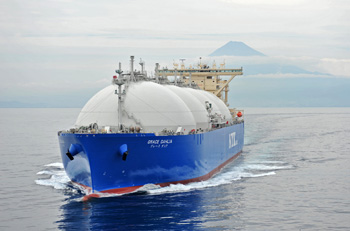
Tokyo, September 30, 2013 — Kawasaki Heavy Industries, Ltd. announced today that it has delivered the LNG carrier Grace Dahlia (Kawasaki hull no. 1665) to Nippon Yusen Kabushiki Kaisha (NYK Line).
This is the second 177,000 m3 LNG carrier to be delivered by Kawasaki, and is the world's largest Moss-type LNG carrier currently in operation. The significant increase in LNG carrying capacity that this vessel offers was made possible by expanding the size of the cargo tanks. Kawasaki has made sure the ship-shore compatibility and outstanding propulsion performance of its existing vessels are not affected by this upgrade.
To power this vessel, Kawasaki has chosen the Kawasaki Advanced Reheat Turbine Plant (Kawasaki URA Plant), which it developed specially for LNG Carriers. This plant is based on a reheat cycle where the steam used in the high-pressure turbine is reheated back in the boiler, and then sent on to drive the medium-pressure turbine. This cycle, combined with a high-pressure, high-temperature boiler, achieves a dramatic increase in thermal efficiency. As a result, fuel consumption is improved by approximately 15% compared to conventional steam turbine plants.
Features
- This vessel features four Moss-type spherical LNG tanks that add up to a total capacity of 177,427 m3.
- The LNG tanks use the Kawasaki Panel System, a high-performance insulation system developed by Kawasaki that keeps the boil-off rate to no more than 0.1% per day.
- The cargo holds housing the LNG tanks employ a double-hull, double-bottom structure to protect the tanks from damage in the case of an accident.
- The pilothouse is equipped with state-of-the-art, network-connected nautical equipment and a satellite communication system, and all information needed for navigating the ship is displayed on a central monitor to enable safe and efficient ship handling. In addition, the pilothouse has windows on all sides to give the operators a 360-degree view.
- Cargo operation is monitored and controlled from the cargo control room situated under the bridge in front of the accommodations, offering a clear view of the loading and unloading area. The cargo control room is provided with an Integrated Automation System (IAS) which gives control over cargo operations and enables centralized monitoring for the main engine as well as cargo. Considerable input from operators based on their actual experience went into the development of this IAS. As such, it is a highly user-friendly system.
- The main boiler of the ship is able to burn Marine Gas Oil (MGO) as an environmentally friendly alternative with low sulfur content. While heavy fuel oil (HFO) is normally used, a pipe arrangement separating HFO and MGO enables switching between the fuels with a simple operation, right before they enter the main boiler's incinerator. Fuel gas can also be used as before.
- Various measures have been put in place to enable cargo transport to cold regions where temperatures reach as low as -25°C. These include the Enclosed Navigation Bridge Wing, ice strengthening that meets ClassNK regulations, air bubbling system to prevent ballast tanks from freezing and other measures to ensure proper operation of equipment below freezing temperature.
- A ballast water management system ensures the ocean habitat is protected from unwanted environmental effects. Further, equipment reliability is enhanced through redundant configurations.
- Lecture rooms with educational facilities as well as accommodations for 20 lecturers and trainees are provided for the purpose of training crew members.
Contact
If you need more information about our business,
please feel free to contact us.