New Factory Completed to Boost Production of Boeing 787 at Nagoya Works 1
Mar. 13, 2015
Tokyo, March 13, 2015 — Kawasaki Heavy Industries, Ltd. announced that it had held a ceremony today to celebrate the completion of a new factory called East Plant on the premises of Nagoya Works 1, which is Kawasaki's aircraft manufacturing and assembly plant. The factory was built to boost the production of the Boeing 787.
The construction of East Plant began in December 2013 on the east side of Nagoya Works 1's South Plant. The plant’s mainstay will be the manufacturing of the Boeing 787-9's and 787-10's forward fuselages. One of the key partners in the 787 Dreamliner program, Kawasaki develops and manufactures the Dreamliner’s forward fuselages, main landing gear wheel wells, and fixed trailing edges, and it has been manufacturing the 787-8 and 787-9 since North Plant was completed in July 2006, and South Plant in March 2010. Just as Kawasaki's other factories, East Plant will house state-of-the-art equipment and machinery to meet increased production of the existing models, and to begin the manufacturing of the 787-10. The new factory is designed for integrated manufacturing that spans from processing composite components to assembling forward fuselages.
The 787 Dreamliner features a number of innovative technologies, such as the world's first one-piece barrel fuselage made entirely of composite materials, part of which Kawasaki manufactures. In early FY2007, Kawasaki shipped out its first 787-8 forward fuselage, and has successfully continued the production since.
Kawasaki continues to increase its manufacturing capacity for the Boeing 787 Dreamliner, and to provide high-quality products. With these contributions to the project as a springboard, the company aims to expand its commercial airplane business.
Overview of the East Plant
Address: 3 Chome-20-8 Kusunoki, Yatomi-shi, Aichi-ken, Japan
Total floor space: Approximately 60,000 m2 (250 m long x 194 m wide x 21 m high)
Main equipment:
1) Autoclave (Cures the composite fuselage. Approximately 9 m in diameter)
2) Automatic fiber placement machine (Co-cures the composite fuselage)
3) Automatic fastening machine (Installs structural components onto the composite fuselage)
4) Trim and drill machine (Drills and trims the composite fuselage)
5) Ultrasonic non-destructive inspection equipment (Inspects composite fuselage quality)
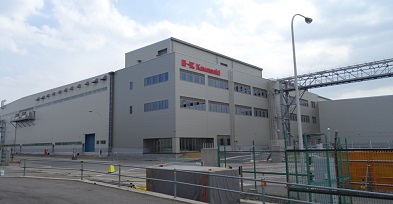
Contact
If you need more information about our business,
please feel free to contact us.